You will discover that nearly every industry around you runs through a SCADA system. It is a system upon which all industrial work largely relies. We can even say that SCADA is an automated control system that gives managers information about the state of the enterprise. It is operated in nearly all industrial verticals to access the whole plant from the control room. Let’s learn more about SCADA and its existence in previous years.
Before SCADA, the Industrial Revolution took a dramatic turn in the form of Industry 3.0, which began with partial automation, with industrialists using memory-programmable controls and computers. During this revolution, the Internet was a breakthrough for everything around us. The invention of computers and software has been hailed as revolutionary and led to task automation, also known as intelligent automation.
About SCADA
The SCADA system is the supervisory control and data acquisition system of software and hardware that allows enterprises to manage processing from regional and outlying locations. It helped industries monitor and control industrial equipment in every segment, like development, manufacturing, production, and fabrication. Many sectors like water, wastewater systems, power, oil and gas, manufacturing, and food production use SCADA systems to collect, monitor, and real-time data. Furthermore, with the introduction of SCADA, it was much simpler to manage industrial processes and directly interact with devices like valves, pumps, & motors.
A basic SCADA system comprises to form a functional SCADA system.
- A human-machine interface is an input-output device allowing a human operator to control the data.
- The supervisory system approach is a communication server that connects the human-machine interface with other equipment like plc and sensor devices.
- Remote terminal units transmit the recorded data to the supervisory systems.
- Programmable logic controllers (PLCs) work through sensors and provide real-time industrial processing monitoring.
- Communication infrastructure
- SCADA programming
How does the Scada system work?
Data Acquisitions:
SCADA systems are essential and reliable because they provide a wealth of data to make intelligent business decisions. Sensors, controllers, and real-time units play an important role in data collection. The real-time system consists of many sensors that collect real-time data. And for the whole system to work perfectly, it is essential to monitor these sensors.
Data Communication:
SCADA uses a wired network for communicating effectively between sensor devices and users. It securely fetches data from sensors for effective data communication and improves efficiency.
Data Presentation:
Since a large amount of data are collected via sensor devices, converting this data into valuable information evolves the most critical task. As it becomes complex to handle a large no. of sensors simultaneously, At the same time, the SCADA system uses a human-machine interface (HMI) to collect all sensor data and convert it into usable information.
HMI:
As SCADA utilizes Human Machine interfaces, the communicated data ought to be observed by humans. It delivers access to numerous control units and PLCs.
Controlling and monitoring :
SCADA systems use controllers to operate each device. These controllers help turn ON/OFF each device, and it works automatically without human intervention, but in specific conditions, it is to handle manually.
Regarding technology, the future of industrial automation is evolving, so robots are replacing people. And now, it is the time for a more extraordinary revolution with the introduction of Industry 4.0
IoT is an evolved concept that enterprises now widely accepted due to sensor-based techniques and data-driven methods. It allows manufacturers to develop their business reasoning and improve their loopholes to serve better quality. For example, if a SCADA system produces complex reports, an IoT solution can improve the format and deliver them more simply and efficiently. Moreover, technology solutions help to share information directly with the head office or any specific person.
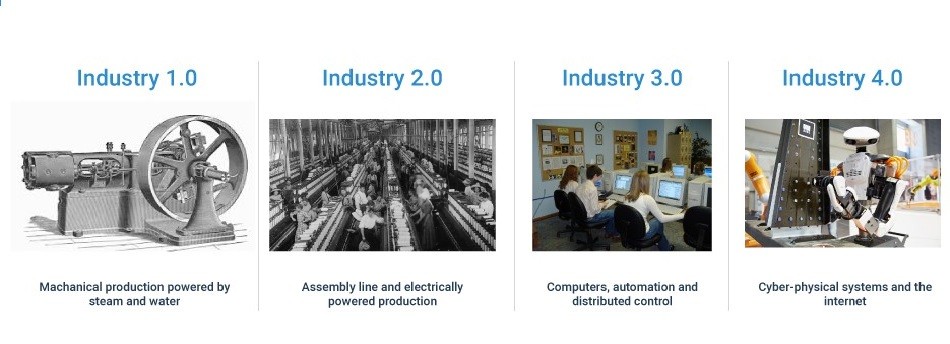
How is IoT Carried over SCADA and PLC?
Programmable logic controller(PLC) is the technology that has been a pal to SCADA Over the past few years. But obsolete because of technical improvement. It can automatically initiate and prevent operations and generate alarms if a malfunction occurs. Even PLCs acquire data from sensors, which process and dispatch it further per the programmed parameters.
Most of the statistics from many industries have concluded that the power of SCADA systems was essential to the Industry 4.0 revolution. Still, it is limited to having an utterly connected ecosystem to handle the rest of the business. However, the Industrial IoT (Internet of Things) has entered the market and has evolved into a superior technology compared to traditional SCADA and PLCs. Undoubtedly, its intellectual capabilities are easily adaptable to today’s modern industries.
The Industrial Internet of Things emerged as a technology implemented on top of SCADA. Parameters such as scalability, and data analytics, appeared with the advent of disruptive IoT technology.
The Internet of Things has brought a wave of new business to change the SCADA landscape. The data generated by SCADA systems is still the data source for Industrial IoT. Industrial IoT focuses on analyzing detailed machine data to improve performance, whereas SCADA used to focus on monitoring and control.
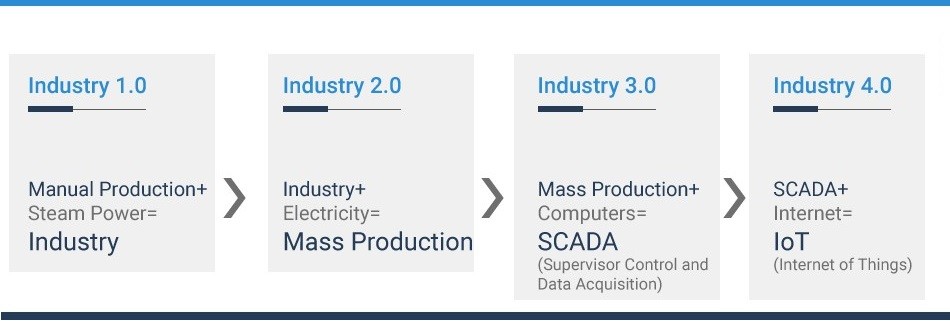
How IoT Differs from SCADA
Features | SCADA | IOT | |
1 | Scalability | In SCADA systems, due to the standard architecture, when the number of users increases, it stains performance drastically. It also carries comprehensive reports from factories in different nations and areas from the significant plant. | IoT can receive and process a vast amount of sensor data and allows you to connect everything that matters using protocols such as MQTT, HTTPS, XMPP, COAP, REST, Etc. which provide on-demand scalability through a serverless architecture |
2 | Data Analytics | The primary SCADA usage is for day-by-day plant operation and ingestion and storage of a finite amount of data without preserving historical data for deeper analytics. | IoT involves long-term data retention to further analyze the data to predict maintenance schedules, reduce overall downtime, and extend equipment life. On top of predictive analysis and preventive maintenance, capabilities are part of it supported by the Machine Learning module. |
3 | Standardization | SCADA systems mainly use Open platform communications to collect data, a model that has stood the test of time. Still, its main disadvantages are DCOM technology and devices cannot contain/exchange data with each other regardless of the footprint. | The main goal of Industrial IoT is to standardize sensor networks, data collection, and aggregation. IoT standards such as OPC UA are already being used to define secure, real-time communications across the enterprise with various control devices and sensors from multiple vendors. Security is built into IoT standards with support for MQTT, HTTPS, RAML, etc. |
4 | Interoperability | SCADA systems cannot be easily integrated with devices from different manufacturers. Sometimes even different versions from the same manufacturer make them difficult to interchange. Thus, SCADA provides distributed business processes that operate independently. | Industrial IoT ecosystems remain fragmented, but protocols such as MQTT allow platforms to connect across all devices, regardless of vendor. |
What will happen next after comparative analysis?
In summary, both SCADA and IoT involve sensors and data acquisition. They differ in many aspects but share a common goal. SCADA is not a complete control system, but the Industrial Internet of Things comprises many interconnected devices. It enables remote control of appliances across different networks and architectures. But integrating IoT with a SCADA system provides a comprehensive understanding of the entire industrial premises more straightforwardly. In SCADA, while you have to generate analytical reports manually, with an IoT-powered solution, you can automate this process to save time and get quality output.